Tier 4 and the Reduction in Diesel Engine Emissions
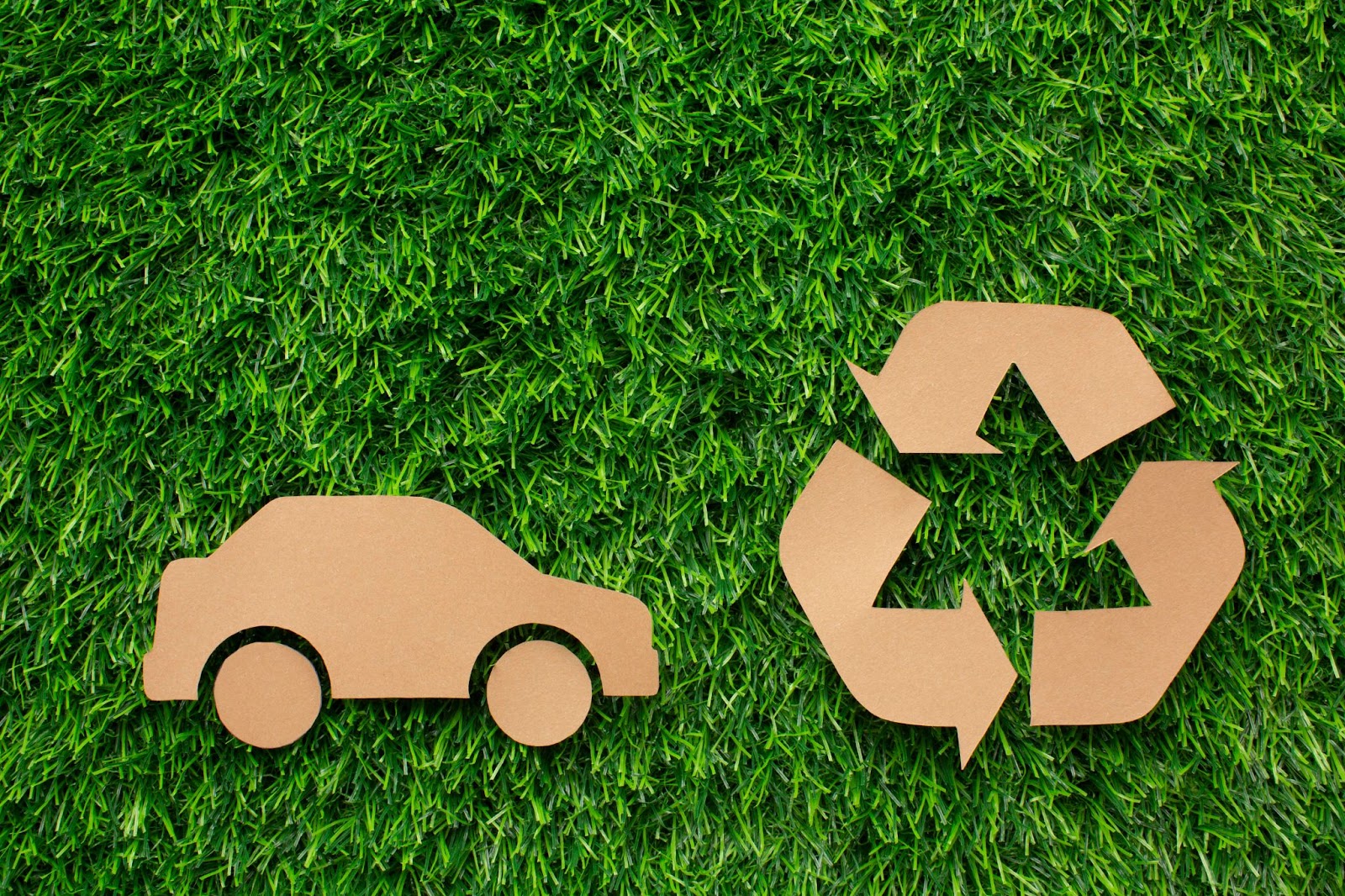
In recent decades, diesel engine emission contaminants have been significantly reduced through various regulations. For instance, high‐power Tier 4 diesel engines used in oil and gas applications emit 80% less particulate matter and 45% less nitrogen oxides (NOx) compared to Tier 2 engines. These reductions not only improve air quality but also translate into considerable financial gains—saving over $30 million in fuel costs. This financial benefit comes as companies enjoy more efficient operations while meeting stricter environmental standards.
Recently, the industry has embraced two primary technologies to achieve these ultra‐low emissions in diesel engines: Selective Catalytic Reduction (SCR) and Exhaust Gas Recirculation (EGR). While there are several technical differences between these two approaches, one key distinction stands out: SCR is considered an after‐treatment solution, meaning it treats the exhaust gases after combustion, whereas EGR is an internal method that reduces the number of pollutants produced during the combustion process by recirculating a portion of the exhaust back into the engine’s intake.
What Is the Tier 4 Engine and How Does It Work?
Tier 4 engines are primarily distinguished by the incorporation of an advanced exhaust gas aftertreatment system. This technology is designed to reduce particulate matter, control soot, lower carbon monoxide (CO) emissions, and decrease the release of nitric oxide by up to 95% into the environment.
This sophisticated aftertreatment system includes a new‐generation fuel supply system that features gas recirculation, an advanced injection system, specialized filters, catalysts, and the use of diesel exhaust fluid (DEF). DEF is crucial because it reacts with exhaust gases to convert harmful pollutants into less harmful substances. Together, these components ensure the engine’s exhaust is properly treated before being released into the atmosphere.
The operation of a Tier 4 engine is both systematic and strategic. It is designed to ensure continuous operation, optimize fuel efficiency, enhance reliability, and extend the lifespan of its components. Moreover, the regeneration technology employed in Cummins industrial and Cummins truck engines facilitates a reduction of up to 8% in fuel consumption compared to previous engine versions. This means that not only are emissions reduced, but overall operational costs are lowered as well.
How to Comply with Tier 4 Standards for Diesel Engines
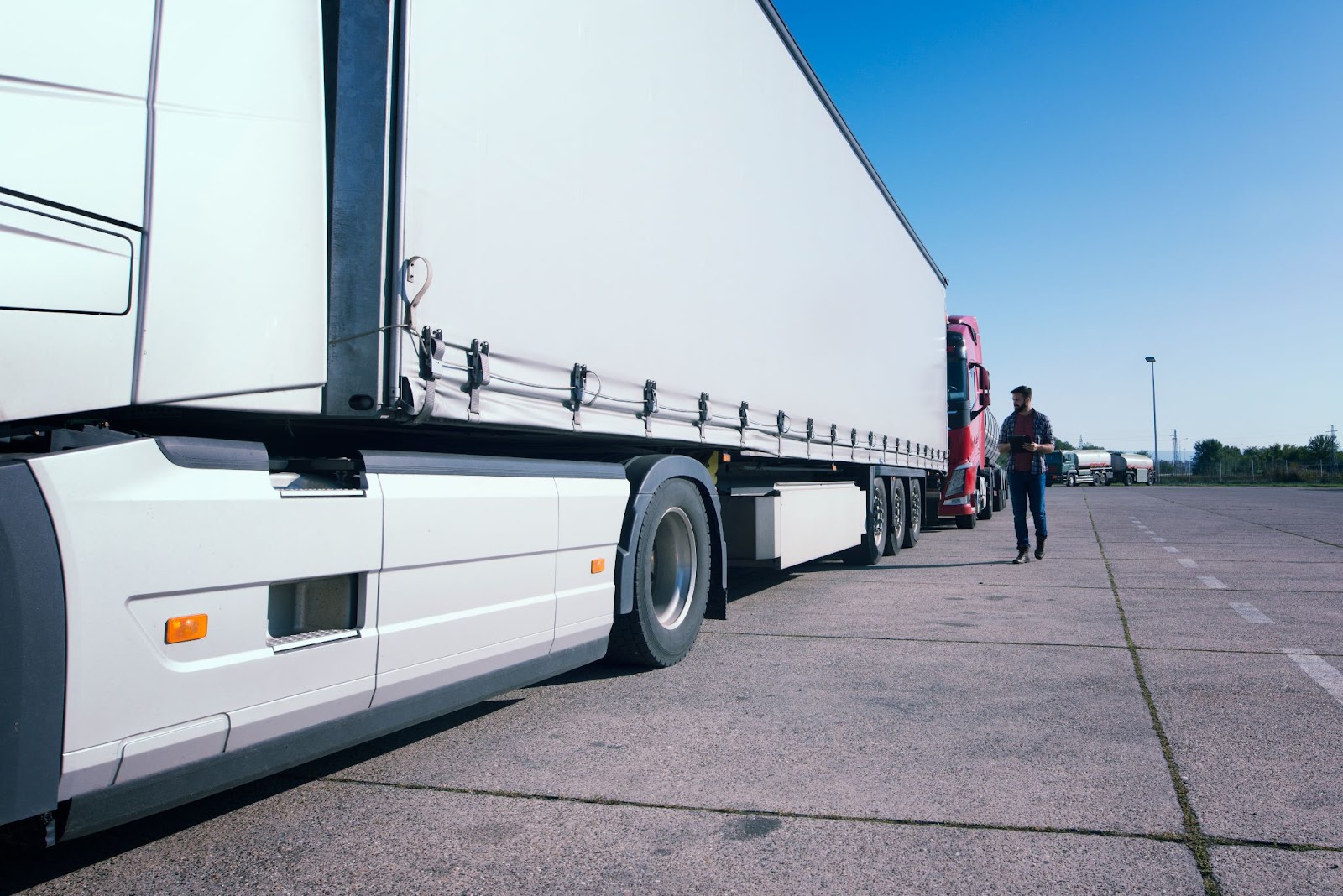
Thanks to advances in engine design, modern diesel engines have become some of the cleanest available today. Improvements such as high‐pressure common rail fuel injection systems, electronically controlled injector solenoids, and advanced turbochargers have enhanced performance and lowered emissions. While these advancements enabled engine manufacturers to meet Tier 2 and Tier 3 standards, adhering to the more stringent Tier 4 Interim and Tier 4 Final regulations necessitated exhaust gas aftertreatment.
There are three main technologies used for the aftertreatment of exhaust gases:
- Selective Catalytic Reduction (SCR): Combines the engine’s exhaust gases with ammonia—delivered in the form of urea or diesel exhaust fluid (DEF)—and passes the resulting mixture through a catalyst. Approximately one gallon of DEF is required to treat twenty gallons of diesel fuel, making SCR a highly effective method for reducing NOx emissions.
- Diesel Particulate Filter (DPF): Functions through a mechanical filtering process that traps soot particles following their partial oxidation by a catalyst. During regular operating intervals, the trapped particles are incinerated in a controlled manner, thereby preventing the buildup of particulate matter in the engine’s exhaust system.
- Exhaust Gas Recirculation (EGR): Recirculates a small portion of the cooled exhaust gases back into the combustion chamber. By doing so, it reduces the combustion temperature and, consequently, the production of NOx. In engines employing EGR, a DPF is typically required to meet the stringent Tier 4 Final regulations.
Benefits of Tier 4 Technology for CAT and Cummins Engines
- Automatic Regeneration: Their regeneration system is fully automatic and intelligent, eliminating the need for operator intervention and ensuring continuous operational performance.
- Enhanced Powertrain Efficiency: The more efficient powertrain helps reduce environmental contamination during operation by ensuring the engine runs more cleanly and efficiently.
- Reduced Operational Costs: With up to an 8% decrease in fuel consumption compared to Tier 3 engines, operators can experience significant cost savings over time.
- Integrated Power and Performance Design: The design, which integrates both power and performance improvements, delivers better overall operational results than earlier engine versions.
- Increased Durability and Engine Life: These engines are built to last longer, with improved durability that reduces maintenance needs and extends the engine’s lifespan.
- Advanced Electronic Monitoring: Advanced electronic management systems allow for continuous monitoring of engine health and operating conditions, ensuring issues are detected and addressed promptly.
What’s Next in Diesel Engine Emission Standards?
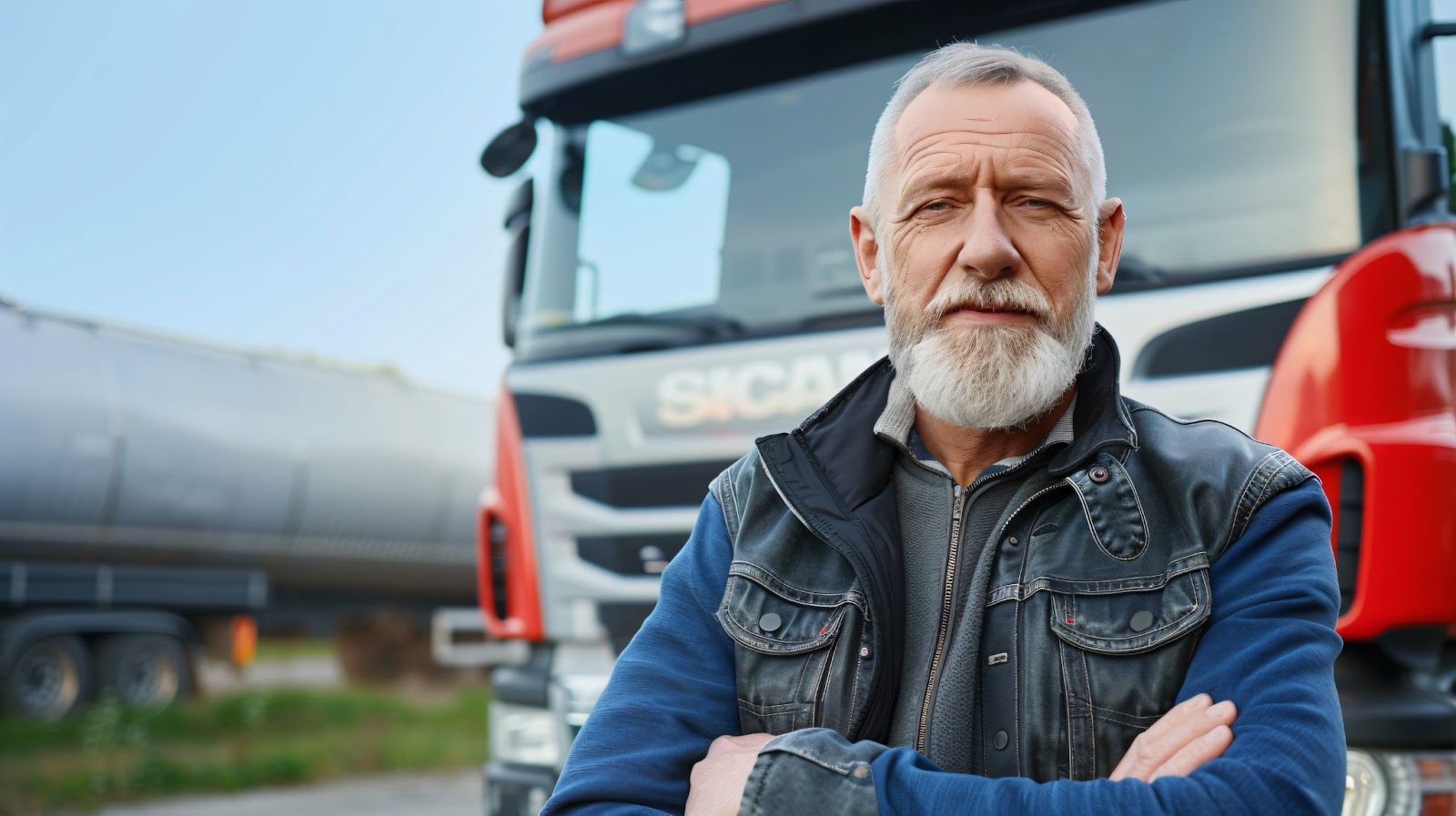
Is there something beyond Tier 4? Yes—Tier 5 regulations are on the horizon. These forthcoming standards are expected to be relatively straightforward to meet with current technology. The primary focus of Tier 5 is to control the ultrafine soot particles in diesel engine exhaust—the submicron particles that pose a significant risk to human health.
Ultrafine particles represent one of the greatest threats to pulmonary health, as they can penetrate deep into the lungs and remain there for extended periods. To combat this, the use of a diesel particulate filter (DPF) in all diesel engines is anticipated. This additional measure will ensure that even the smallest particles are effectively captured and neutralized, reducing the environmental and health impacts of diesel engine emissions.
Pollution Is Illegal: The Clean Air Act
The impact of emission standards on CAT and Cummins engines underscores how technological advancements and regulatory measures are reshaping the diesel engine landscape. The implementation of Tier 4 technology has led to significant reductions in harmful emissions, yielding both environmental and economic benefits.
As the industry continues to innovate, upcoming Tier 5 regulations are poised to address even finer particulate emissions, ensuring that diesel engines remain compliant with the most rigorous environmental standards available.
The persistent efforts to reduce diesel engine emissions serve as a testament to the critical role that regulatory standards—backed by legislation like the Clean Air Act—play in driving sustainable industrial practices. As the global community grapples with the challenges of climate change and air pollution, such regulations are indispensable in the pursuit of a cleaner, healthier future for all.